
These oxides form on the surface of the crucible and must be removed. Regeneration-metal was melted into the crucible to replace lost tin and antimony through the "dross".Įvery time type metal is remelted, tin and antimony oxidise.

If needed, any alloy according to customer specifications could be produced. In Switzerland the compagny "Metallum Pratteln AG, in Basel had yet another
#Typemetal composition manuals#
Type metal alloys mentioned in the UK-Monotype-caster manuals Type produced with these special moulds can only be identified if the foundry or printer is known.
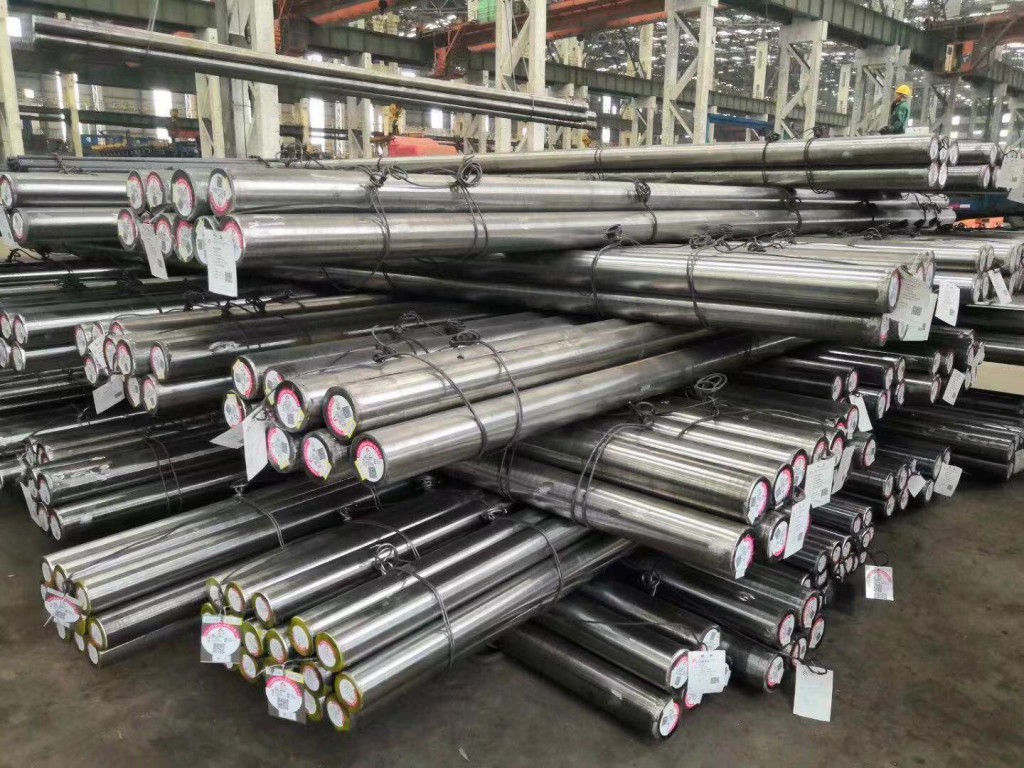
Typefounders and printers could and did order specially designed moulds to their own specifications: height, size, kind of nick, even the number of nicks could be changed. The manuals for the Monotype composition caster (1952 and later editions) mention at least five different alloys to be used for casting, depending the purpose of the type and the work to be done with it.Īlthough in general Monotype cast type characters can be visually identified as having a square nick (as opposed to the round nicks used on foundry type), there is no easy way to identify the alloy aside from an expensive chemical assay in a laboratory.Īpart from this the two Monotype companies in the USA and the UK also made moulds with 'round' nicks. Most mechanical typesetting is divided basically into two different competing technologies: line casting (Linotype and Intertype) and single character casting (Monotype). Typical type metal proportions Eutectic alloy When alloyed with lead, strengthens the alloy and improves casting detail. Improves casting properties by making the molten alloy more fluid.Ĭrystalline appearance, brittle, fusible.
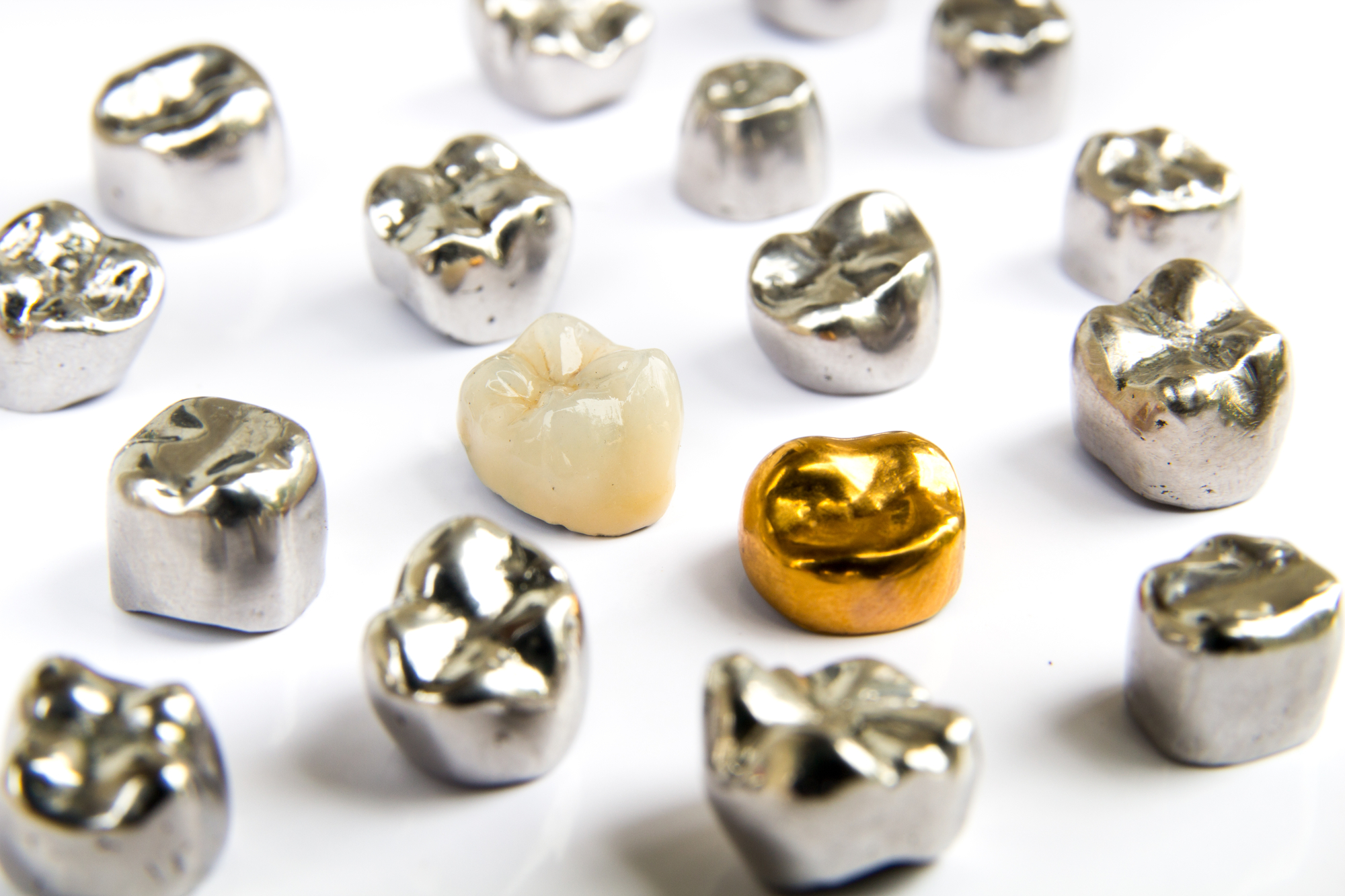
Does not produce sharply defined castings. The basic characteristics of these metals are as follows:Įxceptionally soft, malleable and ductile but with little tenacity. Generally speaking, the proportions are somewhere in the order of: lead 50‒86%, antimony 11‒30% and tin 3‒20%. The addition of antimony conferred the much needed improvements in the properties of hardness, wear resistance and especially, the sharpness of reproduction of the type design, given that it has the curious property of diminishing the shrinkage of the alloy upon solidification.Īlthough type metal alloy are basically conformed by the same three metals, the proportions vary according to the intended final use, be it individual character mechanical casting for hand setting, mechanical line casting or individual character mechanical typesetting and stereo plate casting. Both the iron and the sulphides would be rejected in the process.

The typefounder would typically introduce powdered stibnite and horseshoe nails into his crucible to melt lead, tin and antimony into type metal. The enormous effort to create an alloy with the characteristics needed in an ideal type metal is often underestimated.Ĭheap, plentifully available as galena and easily workable, lead has many of the ideal characteristics, but on its own it lacks the necessary hardness and does not make castings with sharp details because molten lead shrinks and sags when it cools to a solid.Īfter much experimentation it was found that adding pewterer's tin, obtained from cassiterite, improved the ability of the cast type to withstand the wear and tear of the printing process, making it tougher but not more brittle.ĭespite patiently trying different proportions of both metals, solving the second part of the type metal problem proved very difficult without the addition of yet a third metal, antimony.Īlchemists had shown that when stibnite, an antimony sulphide ore, was heated with scrap iron, metallic antimony was produced. (His other contributions were creation of inks that would adhere to metal type and a method of softening handmade printing paper so that it would take the impression well.) The term type metal (sometimes called "hot metal") represents a range of metal alloys that are used in traditional typefounding and mechanical typesetting.Īlthough the knowledge of casting soft metals in moulds was well established before Gutenberg's time, his discovery of an alloy that was hard, durable, and would take a clear impression from the mould (because it did not shrink as much as lead alone when cooled) represents a fundamental aspect of his solution to the problem of printing with movable type.
